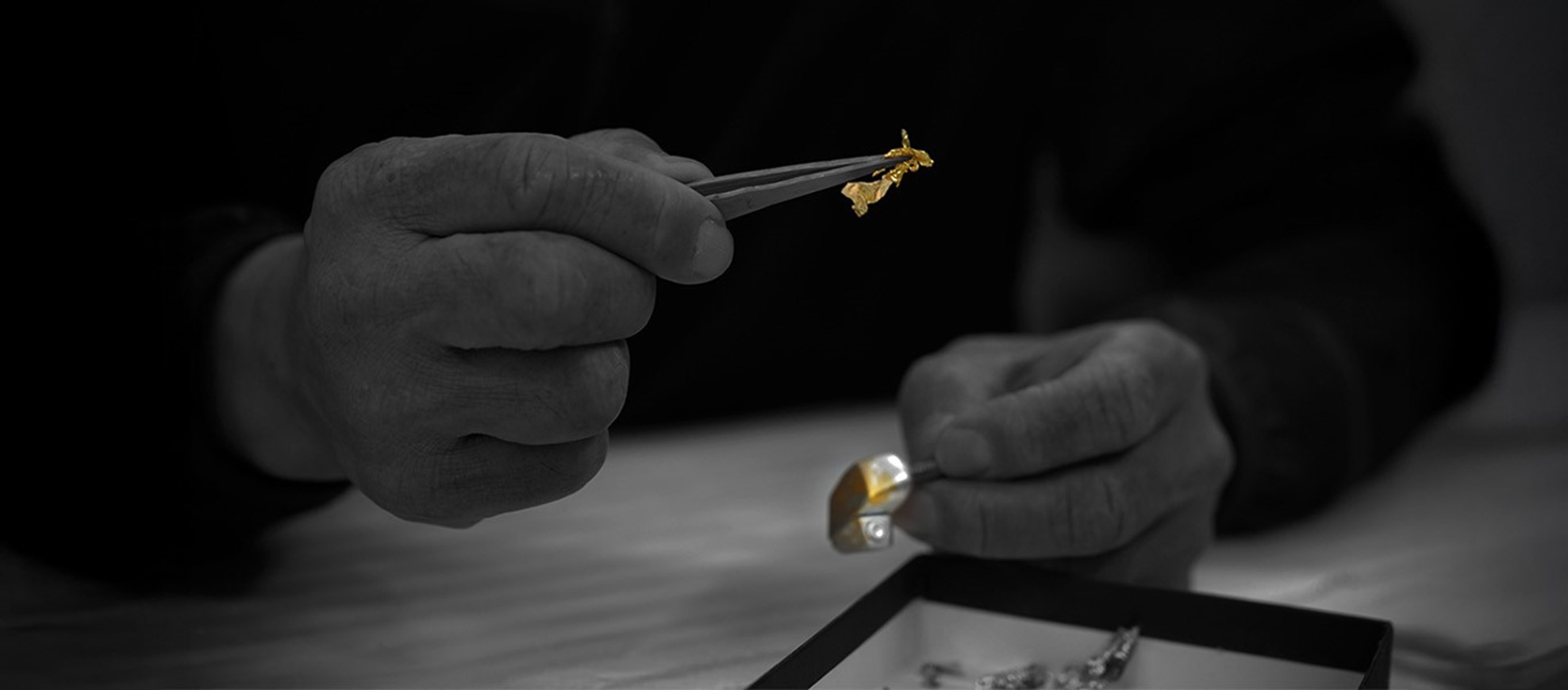
The origins of gold leaf craftsmanship can be traced back to 2000 BCE, with its earliest appearances in mainland China and Egypt. With the spread of Buddhism, this technique was introduced to Japan during the Asuka period (6th century CE). By the Muromachi period (14th century CE), technical innovations in the Kanazawa region led to a groundbreaking leap in gold leaf production. During the Edo period (17th century CE), influenced by Zen aesthetics and the philosophy of “wabi-sabi,” gold leaf was widely applied to everyday objects through gilding, evolving into an art form appreciated by both the elite and the common people. This tradition has continued to the present day, becoming a brilliant treasure of Japanese culture.
The essence of gold leaf gilding lies in perfectly adhering gold and silver leaves, each approximately 10 nanometers thick, to surfaces coated with natural adhesives. Artisans must apply each gold leaf individually with precise pressure, repeatedly folding and pressing to create the desired pattern. Any slight mistake can cause the gold leaf to tear or the pattern to deviate from expectations, requiring the entire process to start over.
Moreover, the technique demands strict control over environmental factors such as humidity, temperature, and airflow, as even the smallest variations can affect the final result. Only artisans with extensive experience, extraordinary patience, and exceptional focus can observe and adjust the placement of each gold leaf under varying light and angles. With the perfect touch, they complete the work to ensure a harmonious and elegant visual effect.
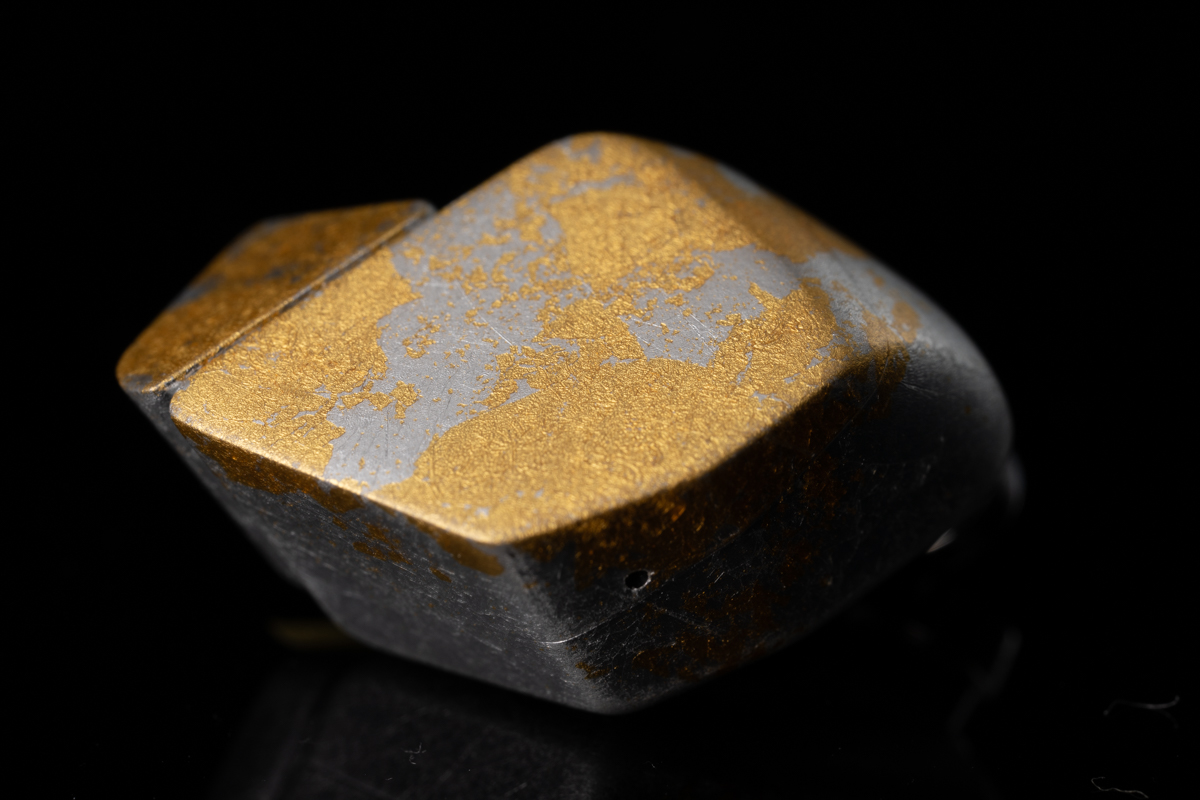
When artisans apply gilding to the A8000 Limited Edition, they approach the process with the spirit of "ichi-go ichi-e" (treasuring each unique moment), carefully layering silver leaf from the center of the earphone outward, repeatedly covering the entire surface. Finally, they add gold leaf as a finishing touch, giving each earphone a distinct appearance and artistic value.
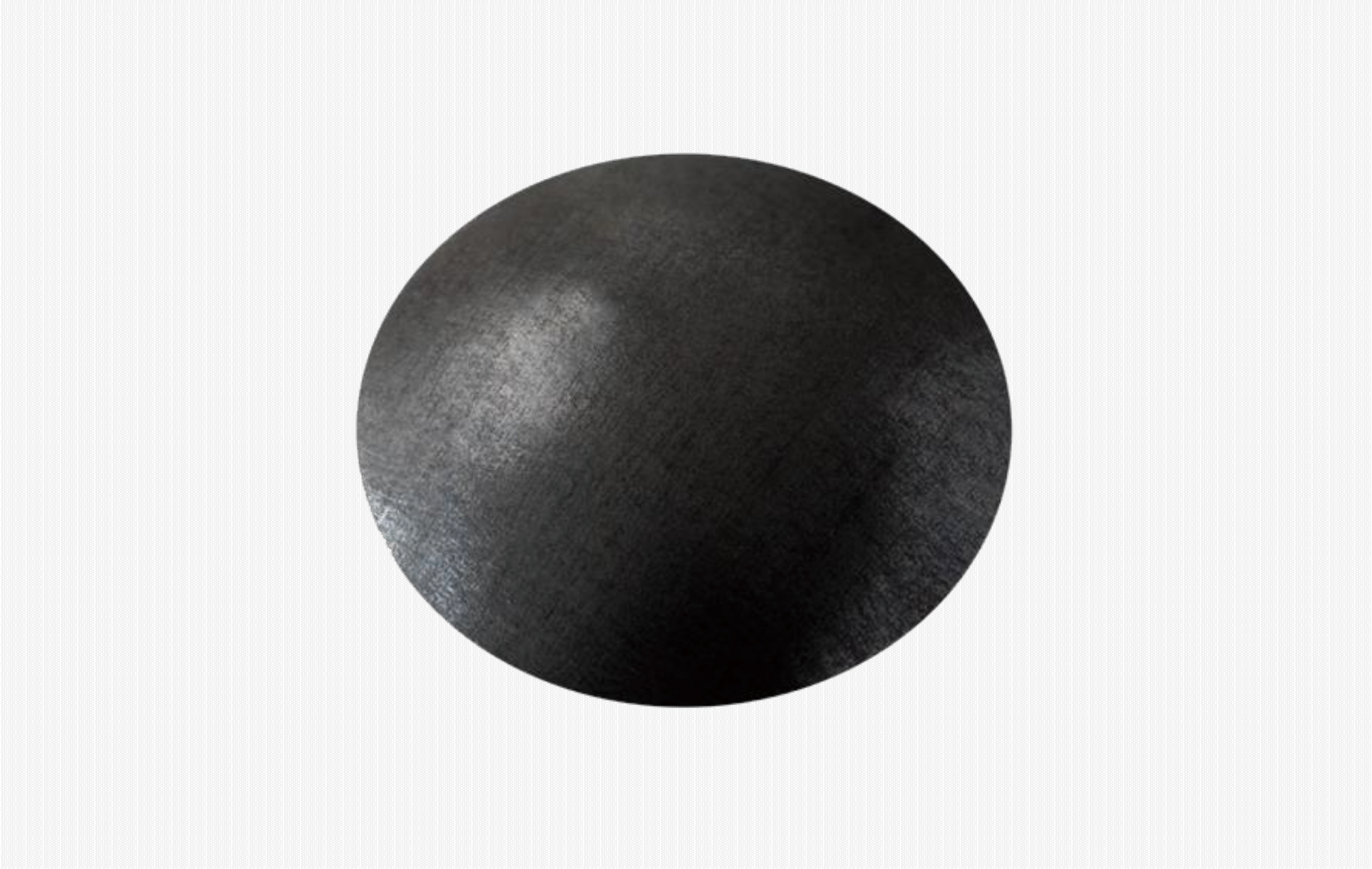
The properties of beryllium make it an ideal material for manufacturing headphone drivers, though it is extremely expensive and processing pure beryllium drivers is highly challenging. In the past, beryllium drivers were typically only found in ultra-high-end speakers or over-ear headphones.
A rigid driver prevents distortion caused by deformation. However, most rigid materials are heavy, and heavy materials cause distortion due to inertia. The advantage of beryllium drivers lies in their exceptional rigidity while being extremely lightweight. This allows them to reproduce fine details in music with high accuracy. Their light weight also enables faster response, resulting in higher fidelity sound reproduction.
In addition, drivers can deform due to standing wave issues at different frequencies. Thanks to beryllium's high rigidity, distortion caused by deformation is significantly reduced, further improving accuracy.
Another key feature of beryllium drivers is their exceptionally high natural resonance frequency. This means that below 20,000Hz, there are no pronounced peaks caused by driver resonance, resulting in a very balanced tonal quality.
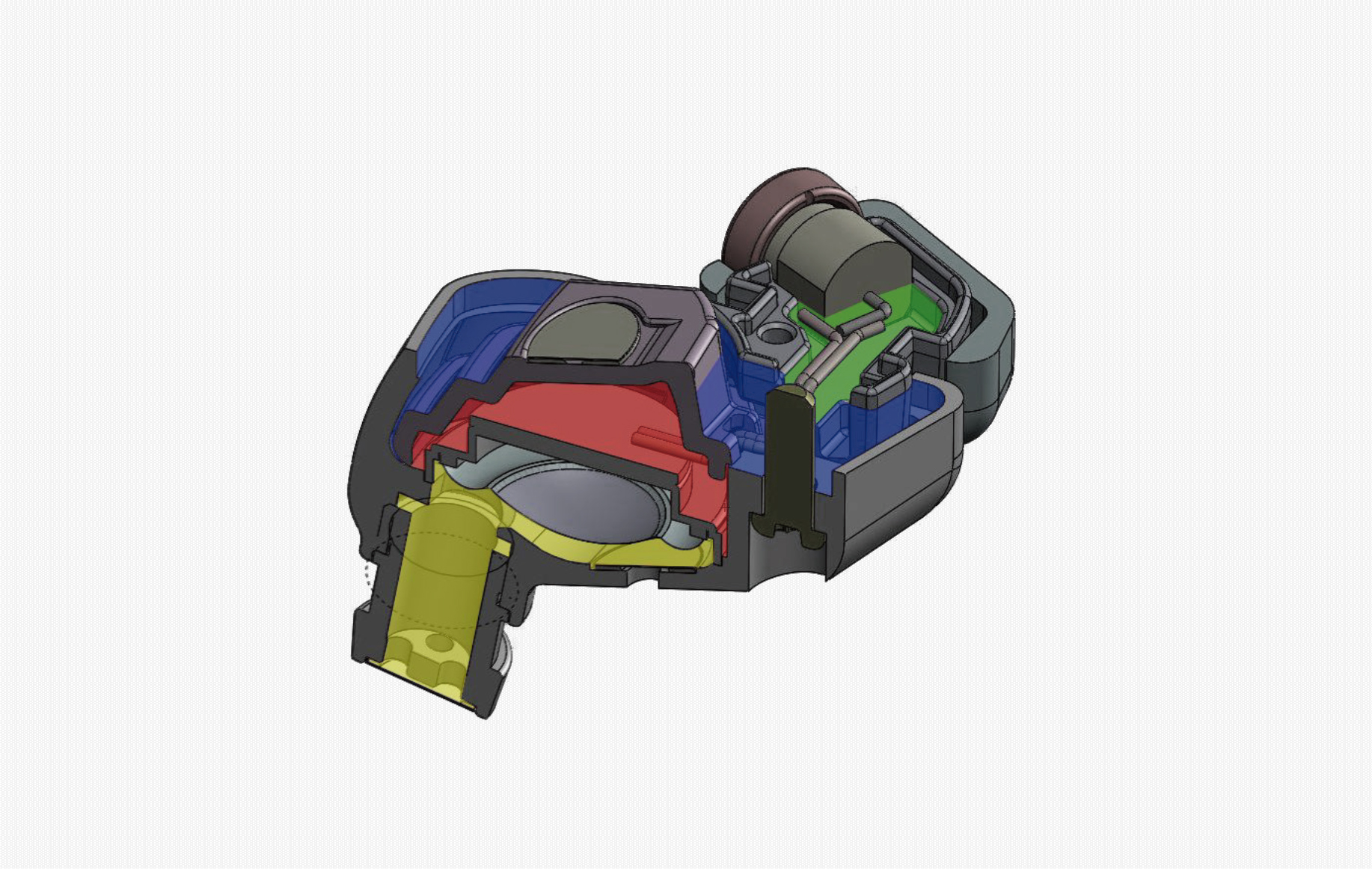
To prevent environmental changes and manufacturing variables from affecting the sound quality, the internal structure of A 8000 is designed into Tetra Chamber Topology with all the 4 chambers are carefully designed to optimize the sonic performance.
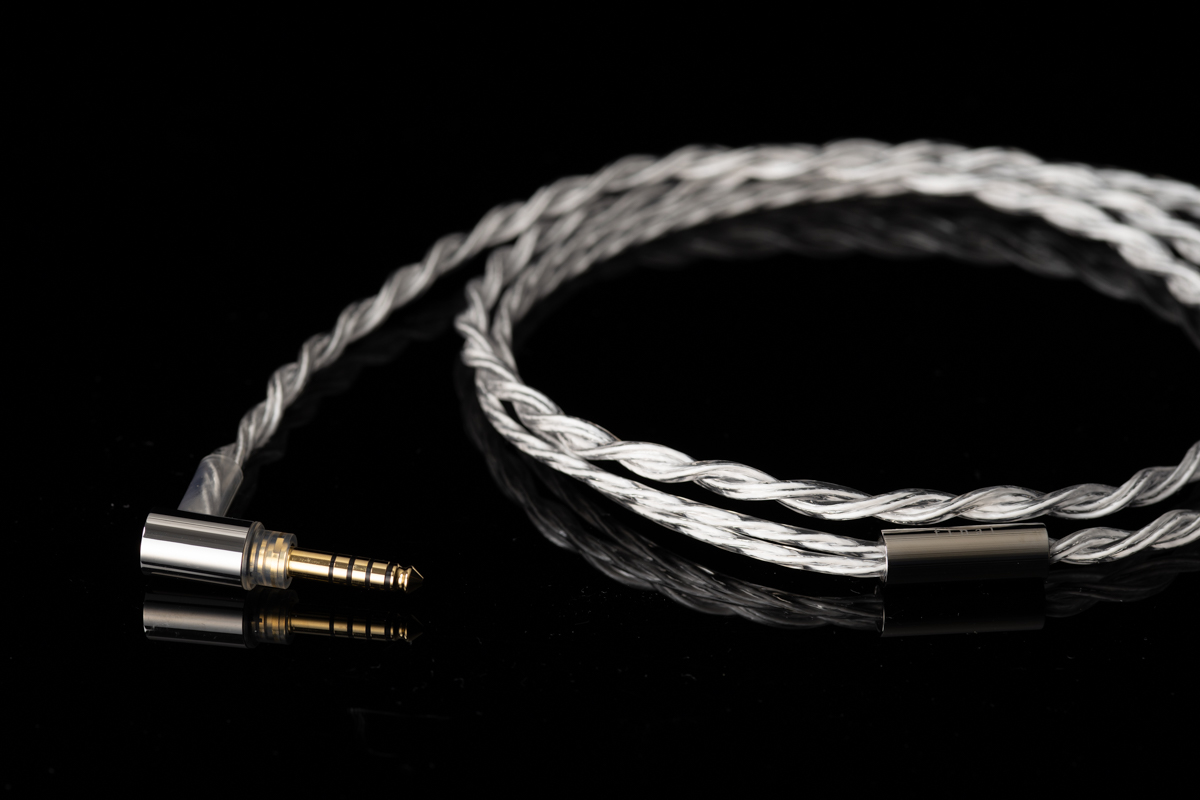
inal has once again teamed up with Junkosha to push the limits of cable technology and further enhance audio performance. The new cable continues to feature a high-purity oxygen-free silver-coated C106 core, while the insulation material has been upgraded from PFA to ePTFE (expanded polytetrafluoroethylene), a material highly acclaimed in the high-end HiFi industry.
Thanks to the foam structure of ePTFE, the contact surface of the wire core is significantly reduced, which dramatically lowers the dielectric constant and capacitive effects of the insulation material. This effectively reduces signal delay and loss, leading to a substantial improvement in signal quality.
Additionally, the overall design of the cable has been meticulously refined, including adjustments to the number of wire windings, their fineness, and the braiding technique, further optimizing its performance.
Specification
Housing:
CNC Machined Stainless Steel Mirror Polished
Driver:
10.8mm Truly Beryllium Dynamic Driver
Sensitivity:
102dB @1kHz
Impedance:
16Ω
Weight:
41g
Manufacturing:
Made In Japan
Welcome to leave your comments for other users' reference